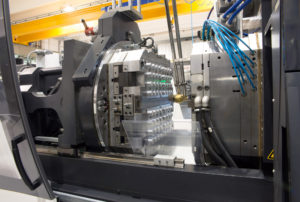
Investing in injection-molded custom OEM cases for your valuable equipment or products provides many individual benefits, but most importantly it ensures the highest level of protection. At S3 Cases, we strive to provide cases that will remain durable in the most extreme circumstances and do so through a commitment to quality from materials through manufacturing and delivery.
What Is the Process for Making Injection-Molded Cases?
Our hard plastic cases are made through a state-of-the-art injection molding process that allows us to produce the highest quality protection for a wide range of applications and industries.
What Is Injection Molding?
Injection molding is a process used to manufacture large amounts of parts and products by injecting heated material into a mold. Injection molding is particularly beneficial for producing products with unique or complicated shaping. In our case, it allows us to deliver products that demand a specific design in order to accommodate items with various shapes and sizes while ensuring strength, durability, and a strong seal. Click here to read more information about what injection molding is.
What Materials Does S3 Cases Use for Injection Molding?
To ensure that our complete line of S3 Cases provides the highest level of protection possible, we use high-impact ABS (Acrylonitrile, Butadiene, Styrene) for all opaque or colored cases and medical-grade polycarbonate for all clear cases. Both of these materials are some of the strongest plastics available on the market. ABS is hard and rigid with outstanding dimensional stability, good chemical and heat resistance, and is also lightweight. Polycarbonate is strong, durable, highly resistant to chemicals, and virtually indestructible.
The Machinery of Injection Molding Manufacturing
Choosing quality materials is extremely important, but in order to produce larger volumes, we also need a high-quality injection molding machine and intricately made molds. The machine is comprised of two high-functioning units: injection and clamping. Molds are made from hollow metal blocks with drilled-in holes to control temperature.
The injection unit of the machine is used to first melt the plastic material, then inject that molten material into the chosen mold. The plastic begins as small pellets that are fed through a heated barrel, using pressure from a rotating screw to push it forward into a cavity. When this cavity is sufficiently filled, the screw uses hydraulic pressure to force the melted material through a nozzle and into the mold. With controlled speed of injection and stabilized dwell pressure, the machine pushes the melted plastic through runners and gates, which ensure that all areas of the mold are properly filled. Once it is sufficiently full, water or a different type of specialized fluid is circulated through a cooling system to extract heat from the mold and cool the plastic material. The mold is then maintained at a higher pressure, allowing it to completely solidify. After the cooling process, the mold is opened and an ejector rod and plate on the injection molding machine are used to expel the molding. To learn more about this process with visual representations, click here.
Advantages of Using the Injection Molding Process
As the molding cools, the next round of plastic pellets is passed through and melted in the heated barrel. This allows for an extremely efficient and fully automated cycle with higher production rates and reduced cost. For our line of S3 Cases, using an injection molding process also allows us to produce intricately and strategically designed cases that will withstand even the most extreme conditions.
The nature of the injection molding process and strict mechanical controls also allow us to deliver a consistent level of quality regardless of the case you get. Injection molding is a very repeatable process with calculated settings, minimizing the risk of error or inconsistencies.
Injection-molded cases are lightweight, yet extremely strong and durable. The ease of production provided through injection molding also creates flexibility in customization, allowing us to produce custom-made cases that are designed to the individual specifications needed to protect your products without excessive overcharging.
The quality of the plastic materials used combined with the process of melting, high-intensity injection pressure, cooling and solidifying result in a case that is resistant to water, dust, temperature, and impact. To read more about the advantages of our injection molded cases, click here.
The Advantages of Injection-Molded Cases
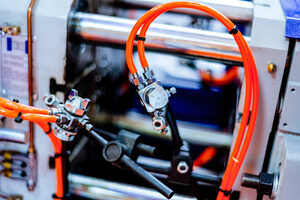
Injection molded cases can be used in a variety of industries, providing a durable and customizable case that will provide the highest level of protection for a number of applications. Whether you need a case for industrial, recreational, medical, shipping, or tactical purposes, injection-molded cases offer a number of features and advantages.
What Is Different About an Injection Molded Case?
Through versatility in manufacturing, injection-molded cases offer a number of benefits and advantages providing a high-quality product for any application.
Ease in Production
The production process is simple, versatile, and cost-effective. Injection molding is also highly efficient, creating a product that is strong and reliable in a quicker time frame. The process, in a nutshell, involves melting high-quality ABS and polycarbonate that is then injected into a mold until it has hardened. This creates the opportunity for automated production that is affordable but also ensures quality through precision. Click here to read more about the advantages of using plastic injection molding for manufacturing of parts.
Lightweight
One of the greatest advantages of injection molded cases is that they are lightweight, making them easy to transport, ship, and travel with. The weight of the case will primarily come from the weight of the product you place within it.
Cost-Effective
Thanks to the efficiency in manufacturing and lightweight properties, injection-molded cases offer industries the benefit of a lower-cost option for a hard-sided protective case. Cases can be custom made to fit a specific product while remaining economical even for large orders.
Strong and Durable
Although these cases are both lightweight and more affordable, it does not mean that they are a low-quality product. Quite the opposite is true. In order to make an injection-molded case, the mold must be placed under extremely high pressure, consequently pressing the plastic to the same level of pressure resulting in a product with enhanced strength and long-term durability. Injection-molded cases offer heavy-duty load-bearing properties with significant impact resistance.
Customizable
Through injection molding, specialty cases can be manufactured for any business application at large quantities. The nature of the production process allows for a case to be custom made to fit the individual specifications for any product and need. The shell of the case along with the foam inserts can easily be made to fit products for any industry. By using a mold, modifications can be made to include the features needed to best protect your product such as hinges or latches, while the high-pressure nature of the process further allows for unique, clearly defined detailing in the shell of the case. Injection-molded cases also provide a number of options in terms of finishes, textures, colors, labeling and more to create a case that reflects the purpose and nature of your products.
These cases are particularly beneficial for original equipment manufacturers (OEM) using molded parts for their products. OEM products are typically not available in standard shapes, making it difficult to fit into standard cases, but with a customized foam insert and custom-sized case, businesses of any nature can find a case to fit the individual needs of their product.
Dust and Water Resistant
Injection-molded cases are also designed to be water-resistant and even dust resistant, offering an even greater level of protection. The materials used are so durable that it can withstand conditions in a variety of environments, reducing the risk of exposure to water, moisture, chemical agents, dirt, dust and more. All of which can cause costly damage to equipment or products affecting function, efficiency, and even appearance. Click here to find out the importance of choosing a dust-resistant case.
Wide Range of Applications
A custom hard-sided case can be very useful for many applications. Their durability and customizable design provide the versatility needed to protect products of all shapes and sizes including:
- Medical Equipment and Supplies
- Tactical Equipment for Military or Law Enforcement
- Audio, Video or Photo Equipment
- Scientific Equipment
- Sporting Equipment
- Industrial Equipment
- Electronics Including GPS, Computers, Radios
- Business Documents
- Financial Documents and Products Including Cash or Credit Cards
- Jewelry
Get Your Custom Injection-Molded Cases
S3 Cases produces custom cases in a range of sizes to meet any application. We have worked hard to perfect the materials, machine settings, and all other variables that are used to produce our cases. At S3 Cases, we offer a lightweight, versatile and extremely durable case with the highest level of protection. We are confident in the quality of our entire line of injection-molded custom OEM cases. Call us today at 970-224-2440 to learn more.